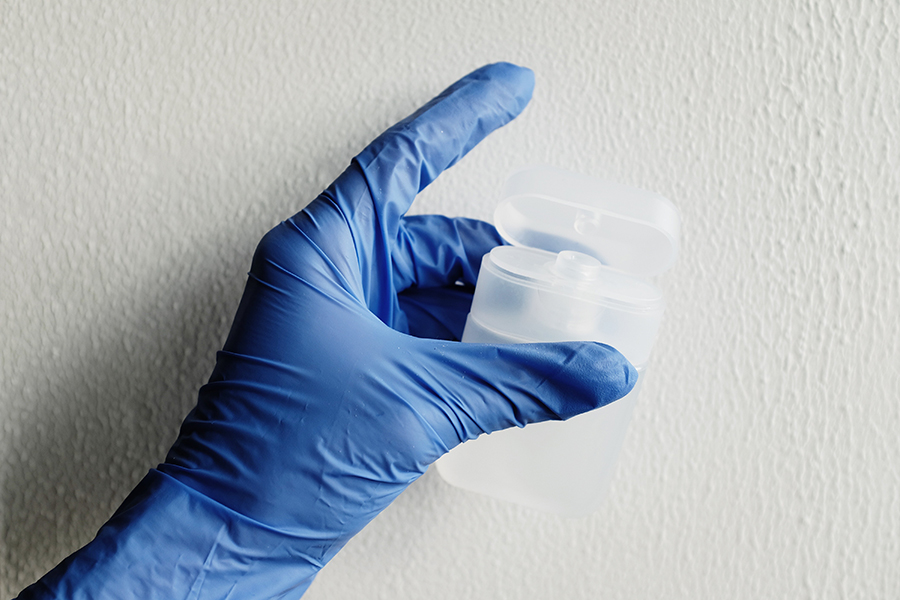
The critical part played by plastics in modern life has never been clearer. From lifesavers such as syringes, medical masks and Personal Protective Equipment to consumer items including disposable wipes, bottles of hand sanitizer and packaging for restaurant meals, this much misunderstood material has proved its worth across all facets of the global response to Covid-19.
To put the plastics value chain onto a more environmentally sustainable footing, one of the world’s largest plastics companies is demonstrating a revolutionary recycling technology that aims to help transform plastics production using the principles of the circular economy.
At an unassuming industrial site in the small Dutch town of Geleen, plastics giant SABIC is using feedstock derived from mixed plastic waste otherwise destined for incineration or landfill to make plastic resins as good as new for major customers such as Unilever and Tupperware.
“Driving the circular economy is vitally important to SABIC,” says Frank Kuijpers, General Manager, Corporate Sustainability at the Saudi Arabia-based petrochemicals company. “We are continuously looking for new means of reusing and repurposing materials.”
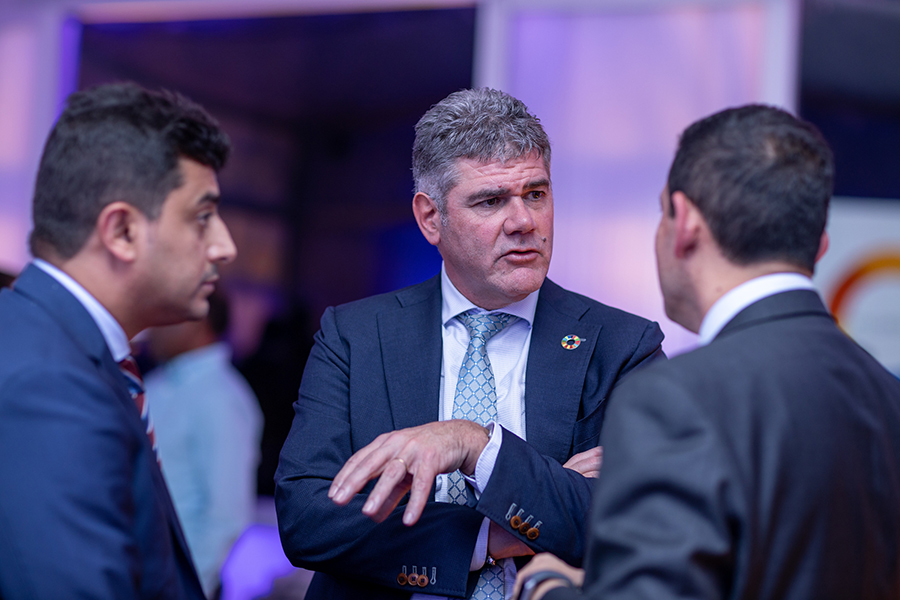
In contrast to the traditional method of collecting, sorting and crushing used plastics, the process used by SABIC chemically breaks down even the most contaminated plastic products into their starting materials. The resulting liquid is then used as a feedstock for making brand-new, high-performance resins. Unlike most recycled plastics, the quality of the end-products is so high that they can even be used in the healthcare, automotive and food packaging industries.
“The process we use at Geleen enables the recycling of a broader range of plastics complementary to mechanical recycling,” Kuijpers explains. “This means that we can replace plastic products based on virgin fossil resources in a wide variety of applications, which is often not possible where mechanical recycling methods are employed.”
Although the technology that SABIC is deploying at Geleen is still early in its development circle, the company has ambitious plans for scaling up the process and aims to produce up to 20,000 tons of recycled plastics from the site by the end of 2021.
At the same time, SABIC is investing in other technologies for collecting, recycling and reusing post-consumer plastic waste. As part of its TRUCIRCLE™ initiative, the company is also increasing its use of mechanically recycled plastics and plastics made from bio-based feedstock and making sure that the plastic resins that SABIC produces are more easily recyclable. By 2025 the company aims to process 200,00 tons of circular or bio-based plastic products in Europe alone.
“We want to accelerate the conversation about the changes we need to make to become a circular global society,” Kuijpers says. “Our vision is to ensure that plastics are always reused and remade into new products.”
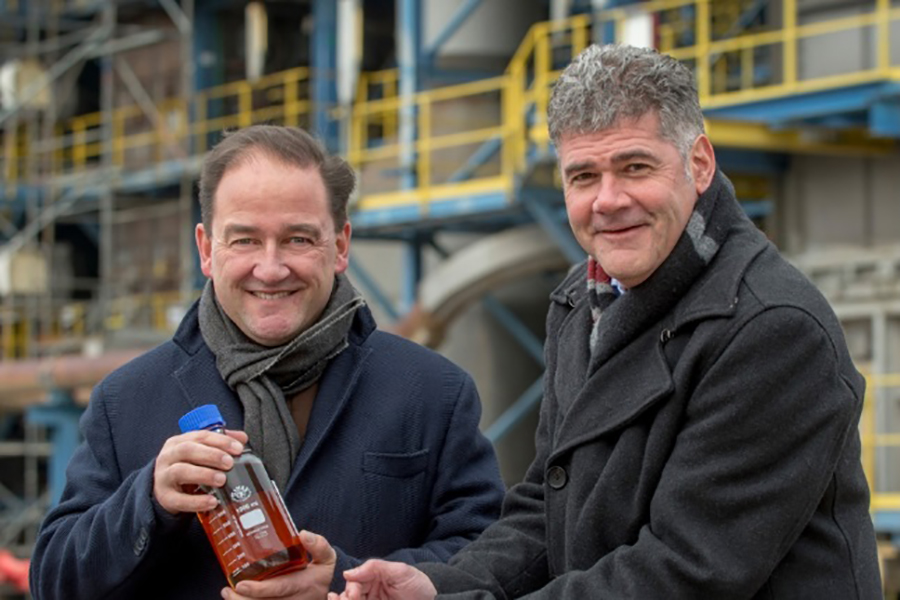
Q&A with Frank Kuijpers, General Manager, Corporate Sustainability, SABIC
How is demand for more sustainable plastics increasing?
SABIC has received unprecedented demand from businesses looking for commercially and environmentally viable solutions which help to address the plastic waste challenge.
The common unifier among these companies is the need to deliver the highest quality packaging solutions without ever compromising on consumer safety, while still being able to meet the environmental and sustainability goals demanded by today’s society.
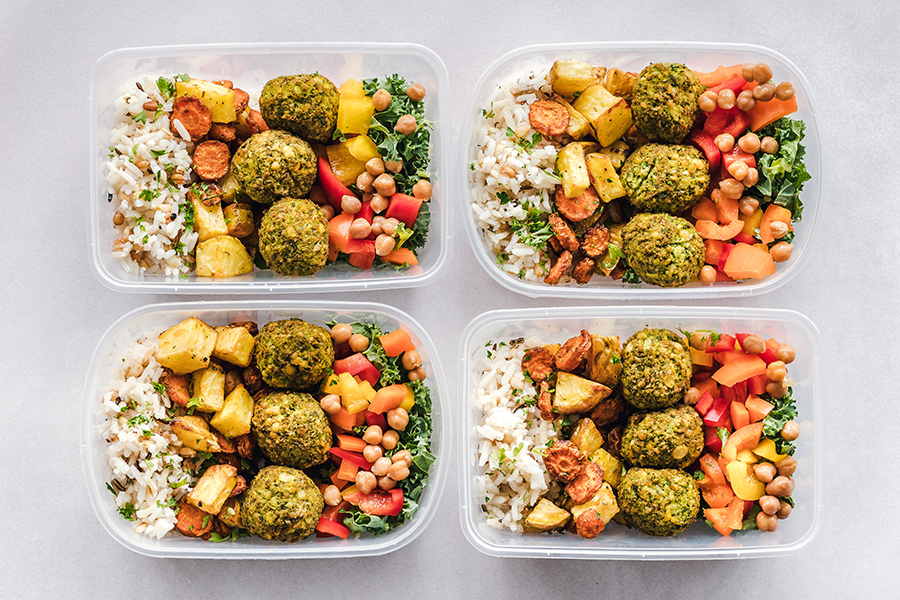
How does the TRUCIRCLE initiative meet this demand?
What’s significant about TRUCIRCLE is the number of consumer products we have enabled brand-leading customers to produce which help to address the plastic waste challenge. This has resulted in a variety of products being launched on the market in the last year made using our range of TRUCIRCLE circular solutions.
We’ve collaborated with a wide range of companies across the value chain to get to where we are today, and there are other organisations who are now ready to join us to close the loop.
“A truly circular economy which meets the needs of our industry, customers and society needs to be one where plastics waste is retained and reused.”
Frank Kuijpers, General Manager, Corporate Sustainability, SABIC
What is the potential of the chemical recycling technology you are developing in the Netherlands?
Chemical (or feedstock) recycling holds the key to reducing the use of conventional approaches of handling end-of-life plastics, such as landfill and combustion. These approaches are outdated as they lock plastics out of reach, destroy future value, and in the case of combustion risk releasing elevated levels of CO2 into the atmosphere.
Chemical recycling enables the recycling of a broader range of plastics than mechanical recycling, but both chemical and mechanical recycling have a positive role to play in driving circularity. Simply not enough single-use plastics are being recycled globally and these two methods complement one another in addressing that.
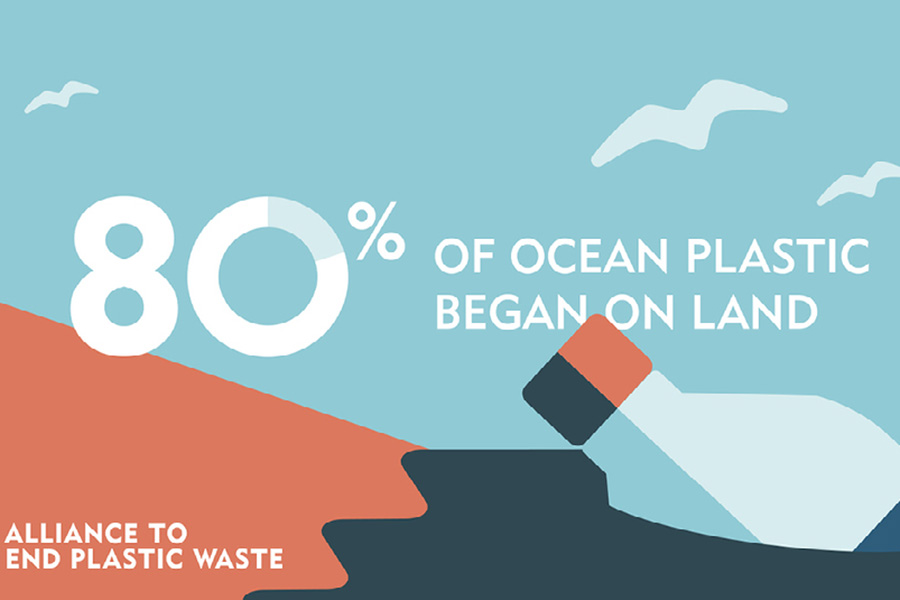
What plans do you have for scaling the facility?
This technology is in its infancy and there are a number of steps required to make the technology truly scalable, so it becomes a more competitive option when compared to virgin polymers. SABIC has new collaborations on the horizon which will allow us to scale up the production of circular products.
How important is sustainability to SABIC and to you personally?
Our CEO has made it clear that our commitment to environmental, social and governance (ESG) issues is just as important to SABIC as our financial performance. We are embracing sustainability and we are adopting a flexible and agile approach to make change happen.
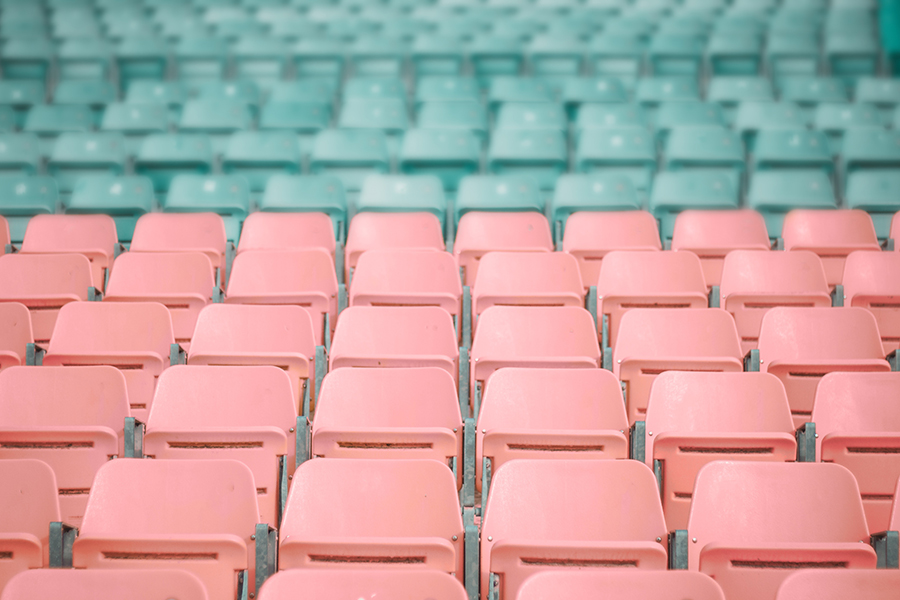
It is very inspiring and exciting to have the opportunity to meet the challenges of plastics today and create a better world, all on the foundations of a strong business case. That is a major driver for me personally and also for SABIC as a global business that is focused on long-term growth opportunities